

PRODUCTS CENTER
The forging plant was founded in 2010 with an initial investment of 230 million yuan, and a production line with an annual output of 500000 forged magnesium alloy wheels, aluminum alloy wheels, and 100T tons of magnesium forgings was built. We have successively passed the IATF16949 quality management system certification, GJB management system certification, and energy management system certification.
Our company currently has three major production lines: forged aluminum alloy wheels, forged magnesium alloy wheels, and magnesium alloy forgings.
Forged aluminum alloy wheels have the characteristics of high strength, strong bearing capacity, good dynamic balance, integrated molding, aesthetics, fuel saving, safety and reliability. Currently, they can produce various commercial vehicles, passenger cars, motorcycles, and military wheels ranging from 16 inches to 26 inches, which are applied to trucks, buses, racing cars, military industries, and customers with the above needs;
Forged magnesium alloy wheels have the advantages of light weight, fast acceleration, reliable braking performance, high comfort, energy conservation and environmental protection. Our company can produce various specifications and patterns of light wheels ranging from 15 inches to 22 inches, suitable for racing cars with high performance requirements, private customization, and special fields with a demand for vehicle lightweight.
Magnesium alloy forgings have the characteristics of low density, high specific strength, good performance, strong thermal conductivity, excellent shielding, and easy recycling. Our company can produce forgings, ring shaped parts, die forgings, conical parts, special shaped forgings, etc. of various magnesium alloy materials within a range of 1000mm, widely used in military industries such as aviation, aerospace, submarines, and various lightweight civilian fields.
The Silver Light Alloy Factory currently has two alloy production lines with an annual production capacity of 20000 tons, as well as two casting rod production lines with an annual production capacity of 7200 tons. It is equipped with advanced magnesium alloy melting equipment and precision production testing instruments, advanced testing methods, and a complete quality system. Currently, it has passed system certifications such as ISO14001, ISO45001, ISO5001, and GJB9001B. The product strictly complies with the international standard GB/T19078-2003, with stable internal quality, high strength, dense internal organization, no shrinkage pores, looseness, solvent corrosion, and no oxide inclusions on the surface and inside.
At present, we mainly produce various grades of magnesium alloys such as AZ series (AZ91, AZ63, AZ31, AZ21, ZM5), AM series (AM50A, AM60B, AMZ40), and AS series (AS31). At the same time, we also produce AZ series (AZ91, AZ80, AZ40, AZ41, AZ31), ZK61, ME20, YGB08, WE43, VW64, and other grades, which can produce cast rods with a diameter of 90-450cm.
Magnesium alloy, as a new environmentally friendly material actively developed in the 21st century at home and abroad, is widely used in the fields of aviation, military industry, and transportation. The products are packaged with wooden pallets and are exported to countries and regions such as Japan, South Korea, the United States, and Europe.
Yinguang Extrusion Factory has a relatively complete extrusion production line in the magnesium industry, with 300T, 800T, 1250T, 1800T, 2500T, and 3600T single action extrusion machines. The equipment has strong capabilities, advanced extrusion processes, and is equipped with heat treatment furnaces with various precision requirements. The improvement of post shaping, straightening, and precision cutting equipment can better provide high-quality services to customers.
The main products include extruded welding wires, extruded wires, extruded rods, extruded pipes, extruded plates, extruded profiles, etc. The products are widely used in magnesium sacrificial anodes, textile industry, electronic 3C, rail transit, passenger vehicles, biomedical, military products and other fields.
The new 10000 square meter modern factory building of the Yinguang Extrusion Plant is equipped with industry-leading 1800T double action extruders, 3600T double action extruders, and the current industry-leading 7500T extruders. It can achieve seamless tube extrusion of magnesium alloys, and the development of ultra wide and ultra large cross-section profiles. It will play a significant role in expanding application fields, expanding the magnesium alloy market, and extending the magnesium alloy deep processing industry chain.
The Silver Anode Factory was founded in early 2000 and has been in production and operation for 20 years. It can now produce 4000 tons of anodes and cast rods annually.
Magnesium sacrificial anode adopts anode protection technology. The main principle is to electrically connect a metal or alloy with more negative potential to the protected metal structure, and provide protection current to the protected object through the continuous consumption and dissolution of electronegativity metal or alloy, so that the metal structure can be protected. Production and testing were carried out using the national standard GB/T17731-2015 for magnesium alloy sacrificial anodes and the national standard GB/T24488-2009 for electrochemical performance testing methods for magnesium alloy sacrificial anodes.
The anode factory can currently produce different specifications of MgMn anodes and AZ63 anode cast magnesium anodes. Its electrochemical performance indicators such as current efficiency and open circuit potential have been tested by authoritative departments and have been recognized. At present, the casting magnesium anode method is used for production, and its shapes are mainly divided into three types: trapezoidal, D-shaped, and rod-shaped (including round and rectangular rods). Common specifications include 17D3, 32D5, and other special-shaped anodes, which can be produced according to customer technical specifications. The produced anode has been widely used in ships, port facilities, marine engineering, buried pipelines, petrochemical, power, municipal and other fields.
The anode factory currently adopts a 3T double-sided heat storage furnace, which has a long heat storage and insulation time, short melting time, and precise temperature control of magnesium liquid. It can better improve the internal quality of the product and fully meet the technical requirements of different customers.
The production method of magnesium cast rods mainly adopts manual casting. Its brands include AZ91D, AM60B, AZ31, MgMn, and pure magnesium, with specifications and models of 60 * 300mm, 90 * 300mm, 92 * 350mm, etc. Its annual output is 1500T, mainly used as raw and auxiliary materials for extrusion products.
Yinguang Plate Factory currently has three magnesium alloy plate production lines, among which the magnesium alloy continuous casting and rolling plate production line can produce magnesium alloy plates with a width of ≤ 600mm, a thickness of 0.3-7mm, and various lengths. The products are widely used in industries such as construction equipment, printing and etching, and can also be used as rolling blanks.
The magnesium alloy hot rolled wide plate production line can produce magnesium alloy plates with a width of ≤ 1500mm, a thickness of 5-200mm, and various lengths; The produced boards have stable quality, large deformation, high strength, and good performance, and are widely used in various fields such as aviation, aerospace, submarines, and automobiles with high performance requirements.
The magnesium alloy coil strip continuous rolling production line can produce thin plate products with a width of ≤ 400mm and a thickness of ≤ 1mm. There are two types of products, sheet and roll, with high accuracy, good performance, strong heat dissipation, excellent shielding, and easy recycling. The products are widely used in industries such as 3C electronics, batteries, electroacoustic equipment, earphone sound film, and medical equipment.
Yinguang Die Casting Factory was founded in 2005 and currently has 3 280T die casting machines, 3 400T die casting machines, 1 630T die casting machine, 1 800T die casting machine, 5 secondary processing production lines, and 4 polishing production lines. We specialize in producing magnesium alloy die castings and can provide one-stop service for die castings. In 2016, it passed the IATF16949 international quality certification. The die-casting factory has many years of profound technological accumulation, particularly skilled in producing structural and airtight parts. The main products include automotive cylinder heads, lampshade brackets, end plate products, electric vehicle wheels and accessories, motorcycle wheels, side plates, electric tool housings, medical device housings, electric balance vehicle accessories, sports equipment, military products, and other magnesium alloy die-casting products in various fields.
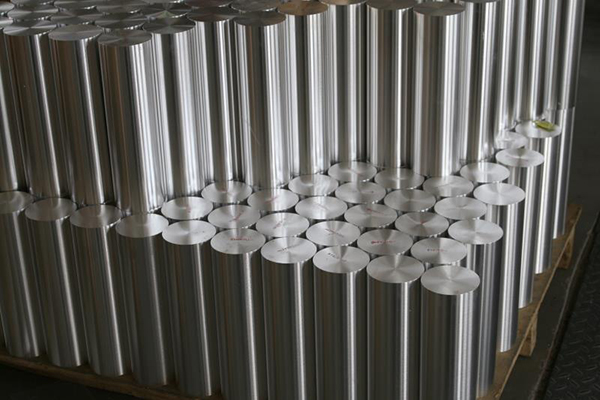
Magnesium alloy bars are alloys composed of magnesium as a matrix and other elements, known as "green engineering structural materials with application potential in the 21st century". They are one of the key new materials developed in the national "13th Five Year Plan" and are widely used in industries such as automobiles, rail transit, military industry, aviation, 3C, biomedicine, electric tools, textile machinery, etc. Processed magnesium alloy semi continuous bars can be used for extrusion, forging After rolling and deformation, the microstructure is finer, the composition is more uniform, the interior is denser, and there is higher strength and high elongation.
Yinguang Bar Factory currently has an 8T hydraulic production line and four 3T vertical screw production lines, with an annual production capacity of 8000T. The production equipment adopts fully automatic temperature control technology, including 11 natural gas furnaces and 4 casting machines. The casting process adopts advanced electromagnetic casting technology and emerging inert gas protection devices. We can produce magnesium alloy cast rods with a diameter of 60-800MM and a length of 6000MM, with over 40 grades including Mg-AL series, Mg-Zn series, Mg-Mn series, Mg-Zr series, Mg-RE series, Mg-LI series, Mg-Gd series, Mg-Y series, etc. The multi specification cast rods of YGB01- YGB26 and other brands developed and produced by Yinguang have been successfully applied in fields such as aviation, aerospace, military industry, 3C electronics, etc.
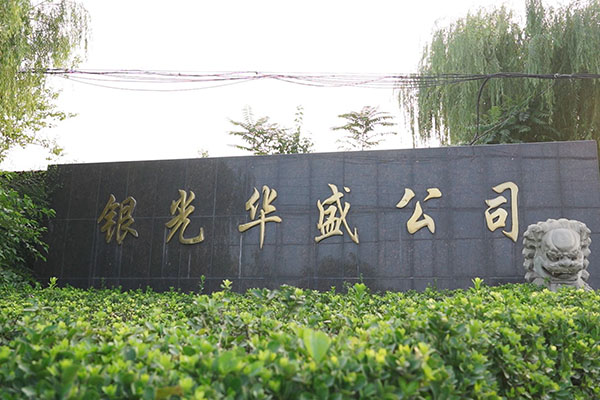
Shanxi Yinguang Huasheng Magnesium Industry Co., Ltd. Liyuan Branch is located in Liyuan Town Industrial Park, Wenxi County. It was completed and put into operation in 2000. Covering an area of 335 acres, with fixed assets of 350 million yuan and over 800 employees.
The company has advanced production equipment, high mechanization, complete testing methods, complete environmental protection facilities, strong technical force, reliable product quality, and has won unanimous praise from customers. It has always been in a leading position in the same industry. The main equipment owned by the company includes 7 sets of two-stage gas generators with a diameter of less than 3.4 meters three point six × Two 54 meter rotary kilns; One 35KV substation; 1 M2480 tube mill, 8 ball pressing machines, and 1 microcomputer batching system; 38 plates of reduction furnace; 20 refining furnaces. The calcination system adopts the basic process structure of advanced preheater rotary kiln vertical cooler. The raw material workshop adopts microcomputer automatic batching, and the reduction section adopts energy-saving and environmentally friendly dual regenerative reduction furnace, which is controlled by computer and mechanized for loading and discharging; The refining workshop adopts automated continuous pouring.
The company has successively passed the integrated certification of quality, environment, and occupational health and safety systems, and has maintained continuous and effective operation in the company, greatly improving the management level of the enterprise. It is one of the top 100 potential development enterprises in Shanxi Province and a Tiger List enterprise in Yuncheng City.
At present, our company's main product is magnesium ingots with an annual production capacity of 40000 tons. The products are widely used in magnesium alloy, aluminum alloy production, aviation and military industry, automotive manufacturing, electronic industry, light industry, chemical industry, instrument manufacturing and other related fields, and are exported to Europe, the United States, Asia and other parts of the world.
PRODUCTS CENTER
The forging plant was founded in 2010 with an initial investment of 230 million yuan, and a production line with an annual output of 500000 forged magnesium alloy wheels, aluminum alloy wheels, and 100T tons of magnesium forgings was built. We have successively passed the IATF16949 quality management system certification, GJB management system certification, and energy management system certification.
Our company currently has three major production lines: forged aluminum alloy wheels, forged magnesium alloy wheels, and magnesium alloy forgings.
Forged aluminum alloy wheels have the characteristics of high strength, strong bearing capacity, good dynamic balance, integrated molding, aesthetics, fuel saving, safety and reliability. Currently, they can produce various commercial vehicles, passenger cars, motorcycles, and military wheels ranging from 16 inches to 26 inches, which are applied to trucks, buses, racing cars, military industries, and customers with the above needs;
Forged magnesium alloy wheels have the advantages of light weight, fast acceleration, reliable braking performance, high comfort, energy conservation and environmental protection. Our company can produce various specifications and patterns of light wheels ranging from 15 inches to 22 inches, suitable for racing cars with high performance requirements, private customization, and special fields with a demand for vehicle lightweight.
Magnesium alloy forgings have the characteristics of low density, high specific strength, good performance, strong thermal conductivity, excellent shielding, and easy recycling. Our company can produce forgings, ring shaped parts, die forgings, conical parts, special shaped forgings, etc. of various magnesium alloy materials within a range of 1000mm, widely used in military industries such as aviation, aerospace, submarines, and various lightweight civilian fields.
The Silver Light Alloy Factory currently has two alloy production lines with an annual production capacity of 20000 tons, as well as two casting rod production lines with an annual production capacity of 7200 tons. It is equipped with advanced magnesium alloy melting equipment and precision production testing instruments, advanced testing methods, and a complete quality system. Currently, it has passed system certifications such as ISO14001, ISO45001, ISO5001, and GJB9001B. The product strictly complies with the international standard GB/T19078-2003, with stable internal quality, high strength, dense internal organization, no shrinkage pores, looseness, solvent corrosion, and no oxide inclusions on the surface and inside.
At present, we mainly produce various grades of magnesium alloys such as AZ series (AZ91, AZ63, AZ31, AZ21, ZM5), AM series (AM50A, AM60B, AMZ40), and AS series (AS31). At the same time, we also produce AZ series (AZ91, AZ80, AZ40, AZ41, AZ31), ZK61, ME20, YGB08, WE43, VW64, and other grades, which can produce cast rods with a diameter of 90-450cm.
Magnesium alloy, as a new environmentally friendly material actively developed in the 21st century at home and abroad, is widely used in the fields of aviation, military industry, and transportation. The products are packaged with wooden pallets and are exported to countries and regions such as Japan, South Korea, the United States, and Europe.
Yinguang Extrusion Factory has a relatively complete extrusion production line in the magnesium industry, with 300T, 800T, 1250T, 1800T, 2500T, and 3600T single action extrusion machines. The equipment has strong capabilities, advanced extrusion processes, and is equipped with heat treatment furnaces with various precision requirements. The improvement of post shaping, straightening, and precision cutting equipment can better provide high-quality services to customers.
The main products include extruded welding wires, extruded wires, extruded rods, extruded pipes, extruded plates, extruded profiles, etc. The products are widely used in magnesium sacrificial anodes, textile industry, electronic 3C, rail transit, passenger vehicles, biomedical, military products and other fields.
The new 10000 square meter modern factory building of the Yinguang Extrusion Plant is equipped with industry-leading 1800T double action extruders, 3600T double action extruders, and the current industry-leading 7500T extruders. It can achieve seamless tube extrusion of magnesium alloys, and the development of ultra wide and ultra large cross-section profiles. It will play a significant role in expanding application fields, expanding the magnesium alloy market, and extending the magnesium alloy deep processing industry chain.
The Silver Anode Factory was founded in early 2000 and has been in production and operation for 20 years. It can now produce 4000 tons of anodes and cast rods annually.
Magnesium sacrificial anode adopts anode protection technology. The main principle is to electrically connect a metal or alloy with more negative potential to the protected metal structure, and provide protection current to the protected object through the continuous consumption and dissolution of electronegativity metal or alloy, so that the metal structure can be protected. Production and testing were carried out using the national standard GB/T17731-2015 for magnesium alloy sacrificial anodes and the national standard GB/T24488-2009 for electrochemical performance testing methods for magnesium alloy sacrificial anodes.
The anode factory can currently produce different specifications of MgMn anodes and AZ63 anode cast magnesium anodes. Its electrochemical performance indicators such as current efficiency and open circuit potential have been tested by authoritative departments and have been recognized. At present, the casting magnesium anode method is used for production, and its shapes are mainly divided into three types: trapezoidal, D-shaped, and rod-shaped (including round and rectangular rods). Common specifications include 17D3, 32D5, and other special-shaped anodes, which can be produced according to customer technical specifications. The produced anode has been widely used in ships, port facilities, marine engineering, buried pipelines, petrochemical, power, municipal and other fields.
The anode factory currently adopts a 3T double-sided heat storage furnace, which has a long heat storage and insulation time, short melting time, and precise temperature control of magnesium liquid. It can better improve the internal quality of the product and fully meet the technical requirements of different customers.
The production method of magnesium cast rods mainly adopts manual casting. Its brands include AZ91D, AM60B, AZ31, MgMn, and pure magnesium, with specifications and models of 60 * 300mm, 90 * 300mm, 92 * 350mm, etc. Its annual output is 1500T, mainly used as raw and auxiliary materials for extrusion products.
Yinguang Plate Factory currently has three magnesium alloy plate production lines, among which the magnesium alloy continuous casting and rolling plate production line can produce magnesium alloy plates with a width of ≤ 600mm, a thickness of 0.3-7mm, and various lengths. The products are widely used in industries such as construction equipment, printing and etching, and can also be used as rolling blanks.
The magnesium alloy hot rolled wide plate production line can produce magnesium alloy plates with a width of ≤ 1500mm, a thickness of 5-200mm, and various lengths; The produced boards have stable quality, large deformation, high strength, and good performance, and are widely used in various fields such as aviation, aerospace, submarines, and automobiles with high performance requirements.
The magnesium alloy coil strip continuous rolling production line can produce thin plate products with a width of ≤ 400mm and a thickness of ≤ 1mm. There are two types of products, sheet and roll, with high accuracy, good performance, strong heat dissipation, excellent shielding, and easy recycling. The products are widely used in industries such as 3C electronics, batteries, electroacoustic equipment, earphone sound film, and medical equipment.
Yinguang Die Casting Factory was founded in 2005 and currently has 3 280T die casting machines, 3 400T die casting machines, 1 630T die casting machine, 1 800T die casting machine, 5 secondary processing production lines, and 4 polishing production lines. We specialize in producing magnesium alloy die castings and can provide one-stop service for die castings. In 2016, it passed the IATF16949 international quality certification. The die-casting factory has many years of profound technological accumulation, particularly skilled in producing structural and airtight parts. The main products include automotive cylinder heads, lampshade brackets, end plate products, electric vehicle wheels and accessories, motorcycle wheels, side plates, electric tool housings, medical device housings, electric balance vehicle accessories, sports equipment, military products, and other magnesium alloy die-casting products in various fields.
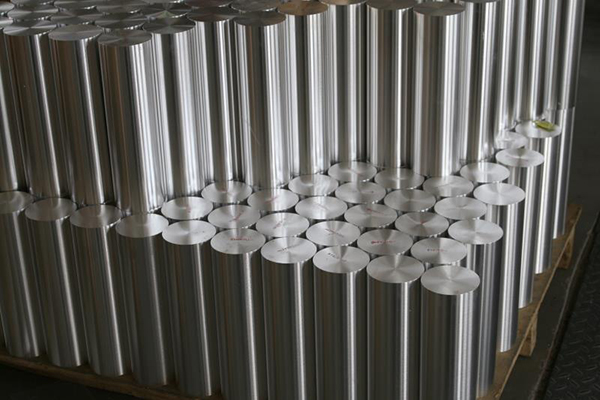
Magnesium alloy bars are alloys composed of magnesium as a matrix and other elements, known as "green engineering structural materials with application potential in the 21st century". They are one of the key new materials developed in the national "13th Five Year Plan" and are widely used in industries such as automobiles, rail transit, military industry, aviation, 3C, biomedicine, electric tools, textile machinery, etc. Processed magnesium alloy semi continuous bars can be used for extrusion, forging After rolling and deformation, the microstructure is finer, the composition is more uniform, the interior is denser, and there is higher strength and high elongation.
Yinguang Bar Factory currently has an 8T hydraulic production line and four 3T vertical screw production lines, with an annual production capacity of 8000T. The production equipment adopts fully automatic temperature control technology, including 11 natural gas furnaces and 4 casting machines. The casting process adopts advanced electromagnetic casting technology and emerging inert gas protection devices. We can produce magnesium alloy cast rods with a diameter of 60-800MM and a length of 6000MM, with over 40 grades including Mg-AL series, Mg-Zn series, Mg-Mn series, Mg-Zr series, Mg-RE series, Mg-LI series, Mg-Gd series, Mg-Y series, etc. The multi specification cast rods of YGB01- YGB26 and other brands developed and produced by Yinguang have been successfully applied in fields such as aviation, aerospace, military industry, 3C electronics, etc.
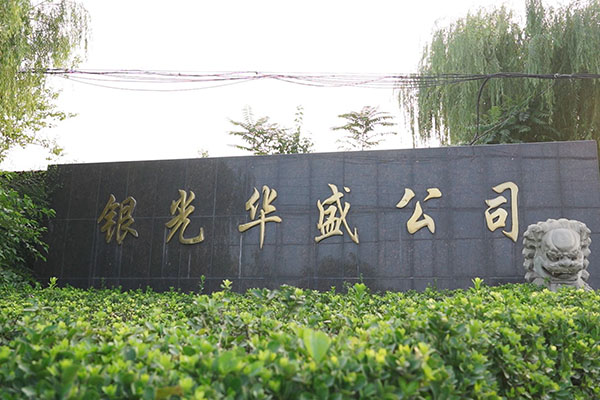
Shanxi Yinguang Huasheng Magnesium Industry Co., Ltd. Liyuan Branch is located in Liyuan Town Industrial Park, Wenxi County. It was completed and put into operation in 2000. Covering an area of 335 acres, with fixed assets of 350 million yuan and over 800 employees.
The company has advanced production equipment, high mechanization, complete testing methods, complete environmental protection facilities, strong technical force, reliable product quality, and has won unanimous praise from customers. It has always been in a leading position in the same industry. The main equipment owned by the company includes 7 sets of two-stage gas generators with a diameter of less than 3.4 meters three point six × Two 54 meter rotary kilns; One 35KV substation; 1 M2480 tube mill, 8 ball pressing machines, and 1 microcomputer batching system; 38 plates of reduction furnace; 20 refining furnaces. The calcination system adopts the basic process structure of advanced preheater rotary kiln vertical cooler. The raw material workshop adopts microcomputer automatic batching, and the reduction section adopts energy-saving and environmentally friendly dual regenerative reduction furnace, which is controlled by computer and mechanized for loading and discharging; The refining workshop adopts automated continuous pouring.
The company has successively passed the integrated certification of quality, environment, and occupational health and safety systems, and has maintained continuous and effective operation in the company, greatly improving the management level of the enterprise. It is one of the top 100 potential development enterprises in Shanxi Province and a Tiger List enterprise in Yuncheng City.
At present, our company's main product is magnesium ingots with an annual production capacity of 40000 tons. The products are widely used in magnesium alloy, aluminum alloy production, aviation and military industry, automotive manufacturing, electronic industry, light industry, chemical industry, instrument manufacturing and other related fields, and are exported to Europe, the United States, Asia and other parts of the world.
